Polycarbonate (PC) Extrusion Manufacturers 10 Q&A
Frequently Asked Questions (FAQ) - Polycarbonate Extrusion Manufacturers
Q1: What is polycarbonate extrusion?
A1: Polycarbonate extrusion is a manufacturing process that involves pushing molten polycarbonate resin through a shaped die to create continuous profiles or sheets. This process is commonly used for producing various products with specific shapes and dimensions.
Q2: What are the advantages of using polycarbonate in extrusion?
A2: Polycarbonate offers high impact resistance than acrylic, optical clarity, and excellent dimensional stability. Its versatility makes it suitable for a wide range of applications, and the extrusion process allows for the creation of complex shapes with consistent quality.
Q3: What types of products can be manufactured through polycarbonate extrusion?
A3: Polycarbonate extrusion can be used to produce profiles, sheets, tubes, and other customized shapes. Common applications include: Construction and Interior Design、Lighting Products、Industrial Applications、Transportation、Electronics、Protective Packaging、Medical Equipment.
Q4: How does the extrusion process impact the optical properties of polycarbonate?
A4: The extrusion process, when performed with precision and proper conditions, ensures that polycarbonate maintains its optical clarity. However, it's essential to follow recommended extrusion parameters to prevent issues such as haze or discoloration. The melt temperature control, cooling rate, mold design and calibration, resin quality, post-extrusion treatment, etc. in the extrusion process are all possible influencing factors.
Q5: What should I consider when choosing a polycarbonate extrusion manufacturer?
A5: When selecting a manufacturer, consider their experience, production capabilities, quality control measures, and adherence to industry standards. Additionally, reviews and references can provide insights into the manufacturer's reputation and reliability. However, SMEACRYLIC have 40 years of experience in PC production and have produced beer tubes, lampshades, pneumatic tube, precision parts packaging, medical equipment applications, etc.
Q6: Can polycarbonate extrusions be customized for specific project requirements?
A6: Yes, many polycarbonate extrusion manufacturers offer customization services.
This includes tailored profiles, colors, and dimensions to meet the unique specifications of your project.
Q7: Polycarbonate tube standard sizes is as below :
Outter Dia. (mm) | Inner Dia. (mm) | Thickness (mm) | Outter Dia. Tolerance | Length (mm) |
5 | 3 | 1 | ± 0.15 | 2000 |
6 | 4 | 1 | ± 0.15 | 2000 |
7 | 5 | 1 | ± 0.15 | 2000 |
8 | 6 | 1 | ± 0.15 | 2000 |
8 | 5 | 1.5 | ± 0.15 | 2000 |
10 | 8 | 1 | ± 0.20 | 2000 |
10 | 7 | 1.5 | ± 0.20 | 2000 |
10 | 6 | 2 | ± 0.20 | 2000 |
12 | 10 | 1 | ± 0.20 | 2000 |
12 | 8 | 2 | ± 0.20 | 2000 |
12 | 6 | 3 | ± 0.20 | 2000 |
13 | 9 | 3 | ± 0.20 | 2000 |
13 | 7 | 3 | ± 0.20 | 2000 |
14 | 10 | 2 | ± 0.20 | 2000 |
14 | 8 | 3 | ± 0.20 | 2000 |
15 | 13 | 1 | ± 0.20 | 2000 |
15 | 11 | 2 | ± 0.20 | 2000 |
15 | 9 | 3 | ± 0.20 | 2000 |
16 | 12 | 2 | ± 0.30 | 2000 |
16 | 10 | 3 | ± 0.30 | 2000 |
18 | 14 | 2 | ± 0.30 | 2000 |
18 | 12 | 3 | ± 0.30 | 2000 |
20 | 18 | 1 | ± 0.30 | 2000 |
20 | 16 | 2 | ± 0.30 | 2000 |
20 | 14 | 3 | ± 0.30 | 2000 |
22 | 18 | 2 | ± 0.30 | 2000 |
22 | 16 | 3 | ± 0.30 | 2000 |
25 | 21 | 2 | ± 0.40 | 2000 |
25 | 19 | 3 | ± 0.40 | 2000 |
28 | 24 | 2 | ± 0.40 | 2000 |
28 | 22 | 3 | ± 0.40 | 2000 |
30 | 26 | 2 | ± 0.40 | 2000 |
30 | 24 | 3 | ± 0.40 | 2000 |
30 | 22 | 4 | ± 0.40 | 2000 |
30 | 20 | 5 | ± 0.40 | 2000 |
32 | 28 | 2 | ± 0.40 | 2000 |
32 | 26 | 3 | ± 0.40 | 2000 |
32 | 24 | 4 | ± 0.40 | 2000 |
35 | 31 | 2 | ± 0.40 | 2000 |
35 | 29 | 3 | ± 0.40 | 2000 |
38 | 34 | 2 | ± 0.40 | 2000 |
38 | 32 | 3 | ± 0.40 | 2000 |
38 | 30 | 4 | ± 0.40 | 2000 |
38 | 38 | 5 | ± 0.40 | 2000 |
40 | 36 | 2 | ± 0.40 | 2000 |
40 | 34 | 3 | ± 0.40 | 2000 |
40 | 32 | 4 | ± 0.40 | 2000 |
40 | 30 | 5 | ± 0.40 | 2000 |
45 | 41 | 2 | ± 0.40 | 2000 |
45 | 39 | 3 | ± 0.40 | 2000 |
45 | 37 | 4 | ± 0.40 | 2000 |
45 | 35 | 5 | ± 0.40 | 2000 |
50 | 46 | 2 | ± 0.40 | 2000 |
50 | 44 | 3 | ± 0.40 | 2000 |
50 | 42 | 4 | ± 0.40 | 2000 |
50 | 40 | 5 | ± 0.40 | 2000 |
60 | 56 | 2 | ± 0.40 | 2000 |
60 | 54 | 3 | ± 0.40 | 2000 |
60 | 52 | 4 | ± 0.40 | 2000 |
60 | 50 | 5 | ± 0.40 | 2000 |
70 | 66 | 2 | ± 0.60 | 2000 |
70 | 64 | 3 | ± 0.60 | 2000 |
70 | 62 | 4 | ± 0.60 | 2000 |
70 | 60 | 5 | ± 0.60 | 2000 |
80 | 76 | 2 | ± 0.60 | 2000 |
80 | 74 | 3 | ± 0.60 | 2000 |
80 | 72 | 4 | ± 0.60 | 2000 |
80 | 70 | 5 | ± 0.60 | 2000 |
90 | 86 | 2 | ± 0.60 | 2000 |
90 | 84 | 3 | ± 0.60 | 2000 |
90 | 82 | 4 | ± 0.60 | 2000 |
90 | 80 | 5 | ± 0.60 | 2000 |
100 | 96 | 2 | ± 0.80 | 2000 |
100 | 94 | 3 | ± 0.80 | 2000 |
100 | 92 | 4 | ± 0.80 | 2000 |
100 | 90 | 5 | ± 0.80 | 2000 |
110 | 104 | 3 | ± 1.00 | 2000 |
110 | 102 | 4 | ± 1.00 | 2000 |
110 | 100 | 5 | ± 1.00 | 2000 |
120 | 114 | 3 | ± 1.00 | 2000 |
120 | 112 | 4 | ± 1.00 | 2000 |
120 | 110 | 5 | ± 1.00 | 2000 |
125 | 119 | 3 | ± 1.00 | 2000 |
125 | 117 | 4 | ± 1.00 | 2000 |
125 | 115 | 5 | ± 1.00 | 2000 |
130 | 124 | 3 | ± 1.20 | 2000 |
130 | 122 | 4 | ± 1.20 | 2000 |
130 | 120 | 5 | ± 1.20 | 2000 |
133 | 127 | 3 | ± 1.20 | 2000 |
133 | 125 | 4 | ± 1.20 | 2000 |
133 | 123 | 5 | ± 1.20 | 2000 |
140 | 134 | 3 | ± 1.20 | 2000 |
140 | 132 | 4 | ± 1.20 | 2000 |
140 | 130 | 5 | ± 1.20 | 2000 |
150 | 144 | 3 | ± 1.20 | 2000 |
150 | 142 | 4 | ± 1.20 | 2000 |
150 | 140 | 5 | ± 1.20 | 2000 |
160 | 154 | 3 | ± 1.50 | 2000 |
160 | 152 | 4 | ± 1.50 | 2000 |
160 | 150 | 5 | ± 1.50 | 2000 |
170 | 164 | 3 | ± 1.50 | 2000 |
170 | 162 | 4 | ± 1.50 | 2000 |
170 | 160 | 5 | ± 1.50 | 2000 |
180 | 174 | 3 | ± 1.80 | 2000 |
180 | 172 | 4 | ± 1.80 | 2000 |
180 | 170 | 5 | ± 1.80 | 2000 |
185 | 179 | 3 | ± 1.85 | 2000 |
185 | 177 | 4 | ± 1.85 | 2000 |
185 | 175 | 5 | ± 1.85 | 2000 |
200 | 194 | 3 | ± 2.00 | 2000 |
200 | 192 | 4 | ± 2.00 | 2000 |
200 | 190 | 5 | ± 2.00 | 2000 |
※ Please click here to
see the specifications of our Extruded Polycarbonate Tube.
Q8: Are there any environmental considerations with polycarbonate extrusion?
A8: Polycarbonate is a recyclable material, and the recycling of plastic helps reduce the need for new raw materials while reducing the impact of plastic waste on the environment. PC is usually marked with recycling number "7". The recycling numbers of other plastics can be referred to as follows:
Q9: How can I request a quote for polycarbonate extrusion services?
A9: To receive a quote, contact us SMEACRYLIC through email:[email protected] provide detailed information about your project, including design specifications, quantities, and any special requirements.
Q10: What quality control measures are in place during polycarbonate extrusion?
A10: SMEACRYLIC implement stringent quality control measures, including regular inspections, testing for physical properties, and adherence to industry standards. Certifications such as ISO9001 can indicate a commitment to quality.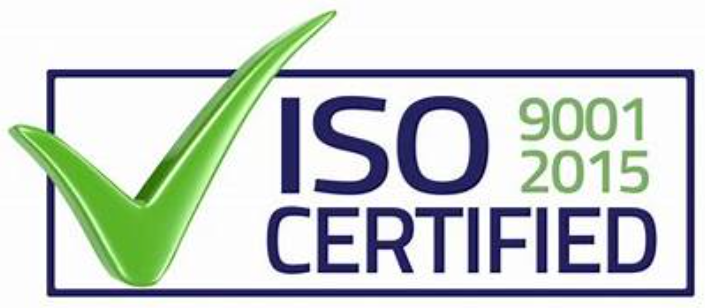
Related Applications
.jpg)
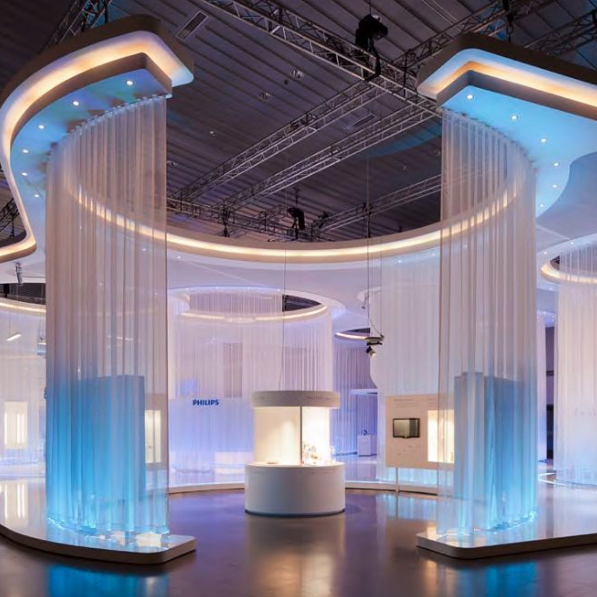
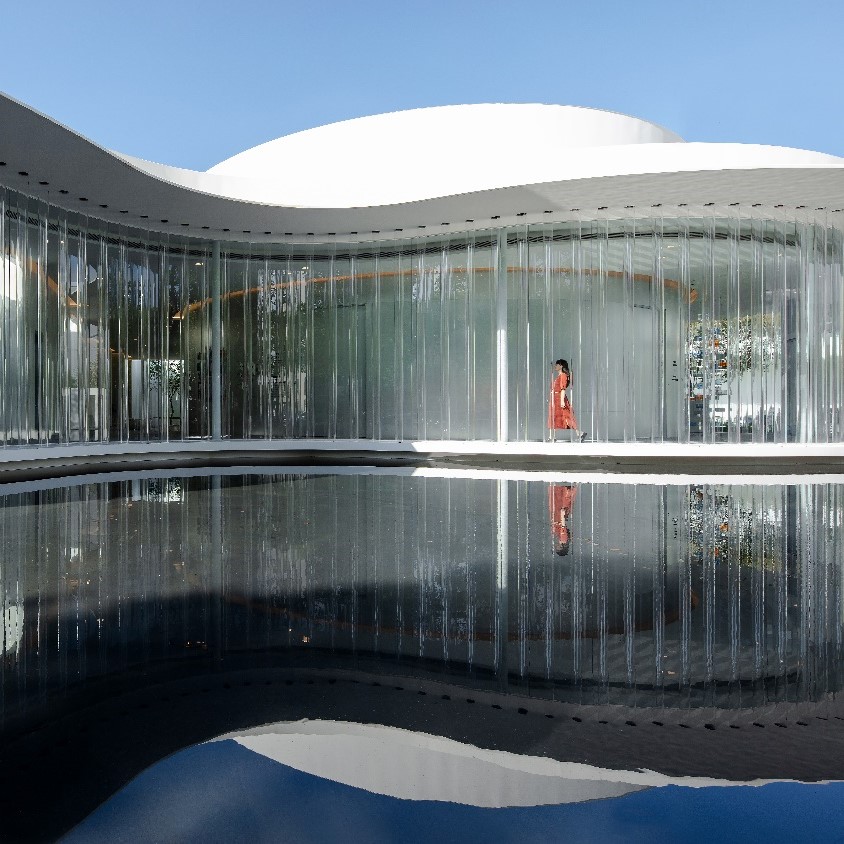
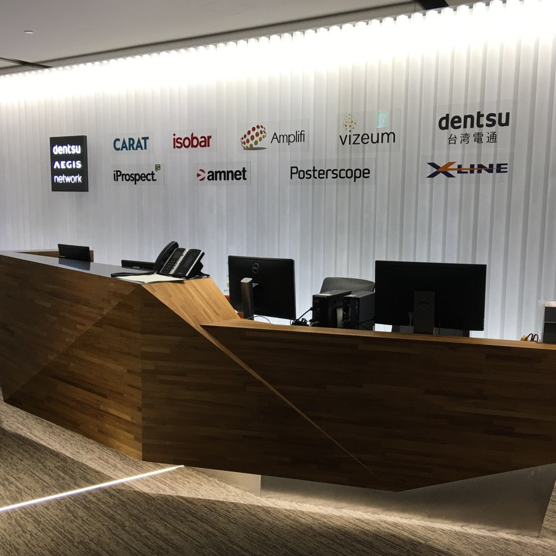
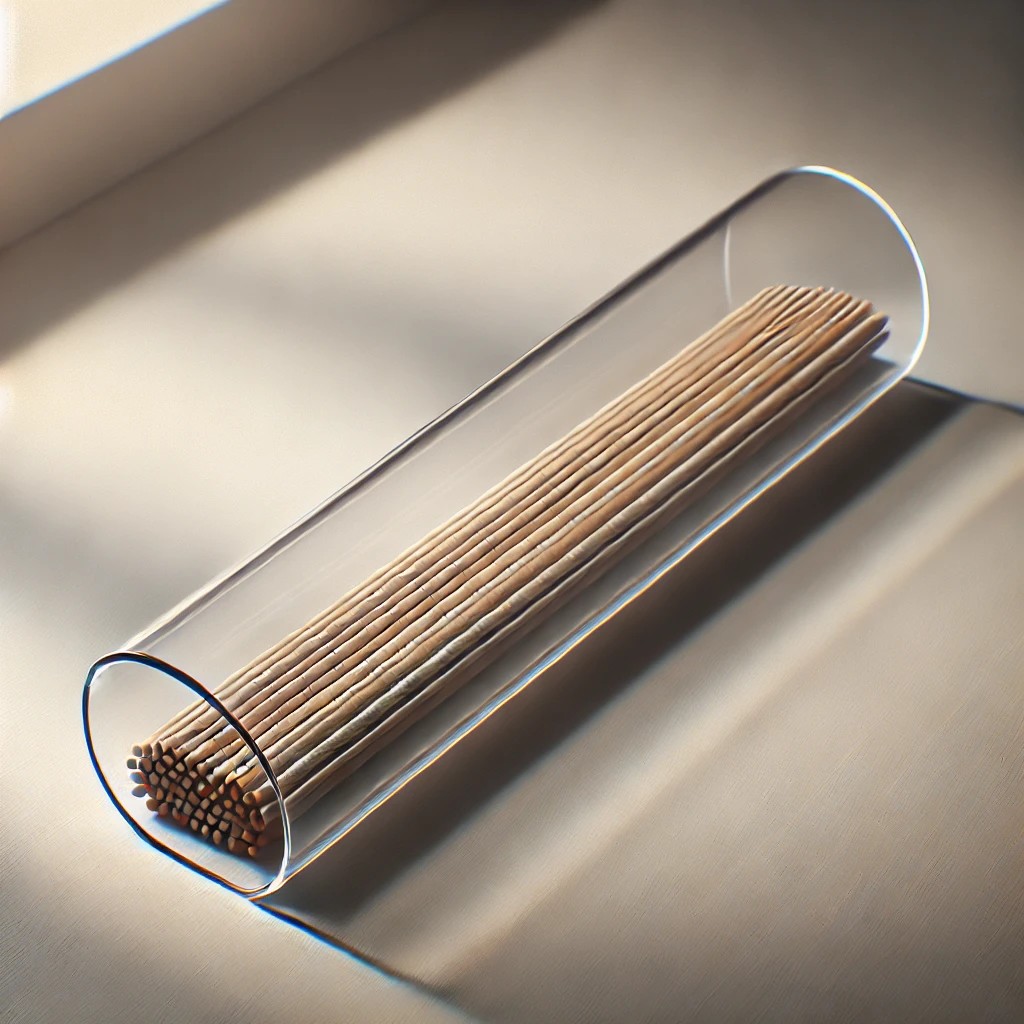